Welding WPS Explained: Trick Components and Perks for Your Welding Procedures
Welding WPS Explained: Trick Components and Perks for Your Welding Procedures
Blog Article
Unlocking the Power of Welding WPS: Strategies for Effectiveness and Security in Fabrication
In the world of fabrication, Welding Procedure Requirements (WPS) stand as the backbone of welding procedures, dictating the needed actions for attaining both efficiency and safety in the construction procedure. Understanding the ins and outs of WPS is critical to harnessing its full capacity, yet several companies struggle to open the real power that lies within these documents (welding WPS). By diving right into the strategies that maximize welding WPS, a world of improved efficiency and heightened security awaits those happy to discover the subtleties of this vital facet of construction

Significance of Welding WPS
The value of Welding Procedure Specifications (WPS) in the fabrication market can not be overemphasized. WPS offer as an essential roadmap that describes the needed actions to ensure welds are performed constantly and properly. By specifying vital specifications such as welding procedures, materials, joint styles, preheat temperatures, interpass temperatures, filler metals, and post-weld warm treatment demands, WPS provide a standardized strategy to welding that boosts effectiveness, top quality, and safety and security in fabrication procedures.
Adherence to WPS assists in achieving uniformity in weld top quality, decreasing the chance of issues or architectural failures. This standardization additionally helps with compliance with industry guidelines and codes, making sure that fabricated frameworks satisfy the required safety and security requirements. Moreover, WPS paperwork enables welders to duplicate effective welding procedures, leading to consistent outcomes across various projects.
Basically, the meticulous development and stringent adherence to Welding Procedure Requirements are vital for supporting the honesty of welded frameworks, guarding against possible hazards, and promoting the reputation of manufacture business for delivering high-quality product or services.
Crucial Element of Welding WPS
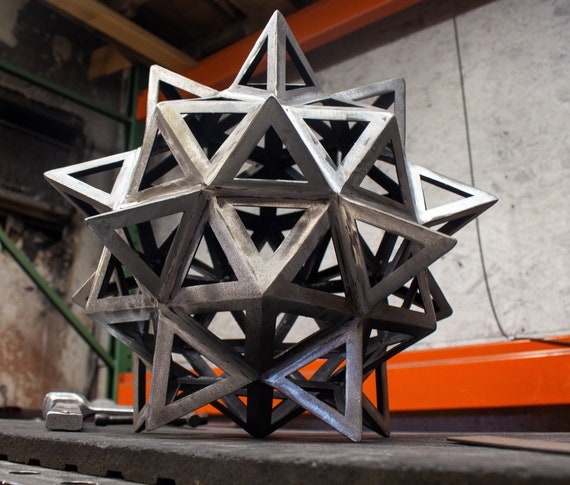
Enhancing Efficiency With WPS
When optimizing welding operations, leveraging the vital components detailed in Welding Procedure Requirements (WPS) becomes important for optimizing and simplifying processes efficiency. One method to improve efficiency with WPS is by very carefully choosing the suitable welding criteria. By sticking to the certain guidelines offered in the WPS, welders can ensure that the welding equipment is established up appropriately, resulting in constant and top notch welds. Additionally, following the pre-approved welding sequences described in the WPS can considerably minimize the time spent on each weld, eventually enhancing overall performance.
Moreover, appropriate training and certification of welders in understanding and executing WPS can further improve performance. Making sure that all team members are well-versed in interpreting and carrying out the WPS precisely can lessen mistakes and remodel, saving both time and sources. On a regular basis examining and updating the WPS to include any lessons learned or technical innovations can also add to efficiency enhancements in welding operations. By welcoming the guidelines stated in the WPS and constantly looking for ways to optimize procedures, fabricators can accomplish greater performance levels and premium end outcomes.
Ensuring Safety in Fabrication
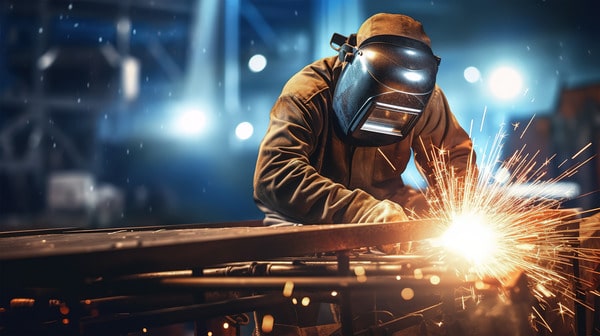
Making certain safety in manufacture involves a multifaceted technique that encompasses various aspects of the welding procedure. Welders have to be equipped with ideal gear such as helmets, handwear covers, and protective garments to reduce risks connected with welding tasks.
Additionally, adherence to appropriate air flow and fume removal systems is important in keeping a healthy work atmosphere. Welding fumes include hazardous materials that, if inhaled, can position significant wellness risks. Implementing efficient ventilation procedures helps to minimize direct exposure to these hazardous fumes, promoting respiratory health and wellness amongst workers.
Regular equipment maintenance and evaluations are additionally vital for guaranteeing safety and security in fabrication. Damaged equipment can lead to crashes and injuries, underscoring the value of routine checks and prompt repair services. click now By focusing on precaution and fostering a culture of recognition, fabrication centers can produce a efficient and protected workplace for their personnel.
Carrying Out WPS Best Practices
To enhance functional performance and make certain high quality results helpful site in manufacture processes, including Welding Procedure Specification (WPS) best methods is critical. Picking the ideal welding procedure, filler material, and preheat temperature level specified in the WPS is critical for attaining the preferred weld high quality. Guaranteeing that qualified welders with the required accreditations carry out the welding treatments according to the WPS standards is vital for uniformity and dependability.
Verdict
In final thought, welding WPS plays an important function in making sure efficiency and security in construction procedures. By complying with these methods, services can open the complete possibility of welding WPS in their manufacture operations.
In the world of construction, Welding Procedure Requirements (WPS) stand as the foundation of welding procedures, determining the essential actions for attaining both performance and safety in the manufacture process. By defining essential parameters such as welding processes, products, joint styles, preheat temperature levels, a knockout post interpass temperatures, filler metals, and post-weld warm treatment demands, WPS provide a standardized strategy to welding that boosts performance, high quality, and safety and security in construction processes.

When maximizing welding procedures, leveraging the crucial components described in Welding Treatment Specifications (WPS) ends up being crucial for maximizing and improving processes performance. (welding WPS)
Report this page